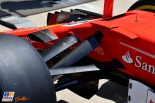
10:04 – Formula 1 regularly involves technical controversy as teams push the envelope to gain an advantage on the track, often exploiting loopholes in the regulations. GPUpdate.net’s technical analyst, Craig Scarborough, looks at some of the attempts undertaken during the 2017 season so far, amid new rules.
Formula 1 has technical controversies every year, from sliding skirts to double diffusers and F-ducts, teams will always push the rules to find a performance advantage, however small that may be. With big rule changes for 2017, and a far greater level of competition between the top teams, the development of the cars has come under greater scrutiny by rivals and the FIA alike. Already this year there have been five major technical developments banned by the FIA and, for some of these, the simple process of the FIA issuing a technical directive has extended into a season-long saga.
Complex suspension
What emerged in the guise of several technical directives over the winter period, a couple of which were at the behest of Ferrari, was in fact a far more protracted investigation by the FIA. Since interlinked suspension (FRIC) was banned in mid-2015, most teams were running simpler systems to regain some of the ride height control lost when they could no longer link the front suspension to the rear.
It is the FIA’s intention that the suspension should be primarily to control the tyre contact patch, and any effect on the attitude of the car for aerodynamic benefit should not be a primary function of the mechanical set up. Already in late 2016 the FIA was inspecting teams’ suspension set-up and finding highly complex systems that were patently not for tyre contact patch control, but rather ride height control for aero benefit. Some systems proved so complex that their actual function was not possible to ascertain from external examination.
As the cars are now all set-up with a raked attitude, nose-down/tail-up, to create more downforce, the cars run very little front ride height. This creates problems with the front of the plank hitting the track and wearing away.
Rather than running very stiff suspension, the springs and dampers are set up to allow a relatively soft ride and soft anti-roll set up, to encourage mechanical grip. But the cars are very stiff under braking, so the effect of the nose diving from the weight transfer is controlled and the plank does not grind away on the track.

To create this soft and then hard suspension control is a tricky task when you cannot use active or FRIC-like technologies. Through 2016 teams were getting very clever with these non-FRIC set-ups, using hydraulics and mechanical links to make the suspension control the ride height. Most of these linked the roll movement to the pitch (or heave) movement, so that when braking in a straight line the pitch control was stiff, but as the car comes off the brakes, turns-in and rolls, the movement in the anti-roll roll switches the heave element to be softer. This was done with mechanical systems like ‘collapsible anti-roll bar links’; many of the midfield teams employed this as it was a cheaper/simpler system than using complex hydraulics. Nonetheless, this was banned over the winter and the technical directive ended up affecting a lot of midfield teams and not just the two or three with far more complex systems.
More concerning for the FIA was the use of passive hydraulic systems to control the ride height. These used fluid lines between the heave element and anti-roll elements, as well as links to separate hydraulic valves and accumulators mounted in the sidepods. In the simplest installation, these merely moved the springing effect under braking to the sidepod mounted hardware, effectively acting as a remote mounted ‘spring’. But with the link to the anti-roll set up and the valving in the sidepod hardware, far more complex control effects became possible. One iteration queried by Ferrari used the movement of the heave element along the straight to ‘pump up’ the accumulator in the sidepod and the pressure built up then used to prevent the nose diving under braking. Other variations of using stored hydraulic pressure were queried and it was largely this that the FIA felt it needed to curb and this in turn affected the top teams, who had developed highly sophisticated suspension set-ups and thus in turn set up their aero philosophy around a tightly controlled ride height window.

With these complex passive systems banned, many teams found the sudden lack of ride height control led them to take a step back in aerodynamic design, as the car could no longer control its attitude to the track so accurately. Therefore the front wing and underfloor had to work in a larger range of ride heights, losing down performance as a result. It appears Mercedes and Red Bull were key losers in this ban, while Ferrari’s questioning of the technologies suggested it was behind the curve in this area. Of all the banned tech, this has been perhaps the most far reaching change and has certainly been a factor in influencing the competitive order of the front three teams.
Oil burning
Unlike the suspension ban, the oil burning technical directive has become a running saga, providing evidence that oil burning is a real performance factor with the current engines. During winter testing a technical directive went out explaining that excessive consumption of oil was not acceptable, as it was apparent that oil was being used as part of the combustion process. An oil consumption limit of five litres per race was imposed. This directive was subsequently updated several times throughout the year as teams continued to exploit oil burning.
When we talk about oil burning in F1, this is not using oil directly as a fuel, rather using the oil as a means to introduce additives into the combustion process that are not allowed in the petrol. This means that when the engine is being pushed hard, the management of heat and the effect of knock can be better controlled, leading to a more powerful engine.

Through 2016 the FIA had an eye on oil burning; while a race engine will always blow out and burn a lot of oil compared to a road car engine, the race oil consumption of five litres was seen as excessive. To put this into context a typical road car engine carries five litres of oil and if in good condition should lose very little of it between services. In contrast, it was found that the F1 cars were losing a shot glass of oil per lap!
Thus the link between oil consumption and special engine maps was clear and the FIA stepped in to preserve the concept that F1 engines should be burning petrol, not oil. The initial directive of a five-litre oil consumption per race was ineffective, as the high oil rate mappings were used not for the duration of the race, but rather in qualifying and tactically during races for overtaking/defending. As a result, the directive was updated to specify a lower specific consumption rate, thus the race oil capacity was reduced and high oil consumption for qualifying could be monitored.
The process of oil burning is quite simple: the oil in the bottom end of the engine is thrown around by the engine’s reciprocating parts, creating an oil mist. The FIA also allows an active system for the oil mist in the crankcase to be vented into the airbox. Thereby it is a simple method for the specially formulated oil to be sucked into the engine and burned along with the fuel and air. This releases the additives to make combustion more effective and thus creates more power.

As this venting system is legal in principle, it can be adapted for certain engine maps, less oil mist being vented for low power engine maps and more for qualifying. Under the second directive, oil consumption was limited to 1.2 litres per 100km until Monza. Thereafter it had to be at a maximum rate of 0.9 litres per 100km, knocking quite an amount of potential power from the oil burning system.
In the midst of this a technical directive at Baku further complicated the saga, when Ferrari was reportedly found to be running an extra oil tank and within it a different oil formulation to that in the main oil system. This was widely understood to be Ferrari’s response to finding an oil burning advantage: using a different oil during laps with the high-power map, allowing the special oil formulation to pass into the combustion process. However, it has never been sufficiently explained quite how this process works. Any oil released from the secondary tank must either find its own way into the airbox or be mixed with the normal engine oil and thus weakened. Both are complicated processes and while possible do bring a question mark as to how or if Ferrari used this system. Regardless, the FIA directive was that only one formulation could be run at a time, so a second tank with different oil could not continue to be used.

As Monza and the tighter oil consumption rate approached, the rule demanded not that every engine must consume less oil, but only new specifications of the V6 engine. Clearly the argument from the teams is that the engine is designed with a specific oil consumption target, and to reduce that would make the unit unreliable. Therefore teams would be able to continue run older specification engines with the high oil rate.
Mercedes was able to bring a new specification to Spa that allows them to run it at the higher oil consumption (1.2 litre/100km rather than 0.9 litre/100km) if it wants to for the remainder of the season. Thus, it retains all the oil burning power advantage, while none of its rivals could bring a pre-Monza spec, and any new engine introduced from now on will have to be done with the revised oil rate taken into account.
To conclude, the effect on oil burning appears to have hindered Ferrari more than Mercedes, which is ironic given the practice has been best exploited by Mercedes in recent years.
An in-depth oil-burn feature will be published ahead of the Singapore Grand Prix
Ferrari’s blown axle
An aero trick raced since 2012 has been the blown front axle. This uses the brake ducts to purposely direct air out through the hollow front axle, though not for any cooling or braking effect. Instead, this is part of the front wing’s efforts to push the turbulent front tyre wake away from the rest of the car. This outwash effect created by the blown axle and front wing endplate helps keep the rear wing and diffuser in clean air, allowing them to work more efficiently. If the tyre wake is allowed to hit the rear bodywork, then less downforce will be created.

Many teams have run these blown axles since Red Bull introduced them, and have simply become another trick in a team’s aero-armoury. There has been nothing remarkable or interesting in their development in the past few years. However, another FIA technical directive released mid-season was aimed at Ferrari and its ducting system, allowing the axles only to be blown in turns.
That Ferrari could achieve this, in a potentially legal way, came as a big surprise to other teams and media alike. Additionally, there were questions as to how it was able to keep this secret, when the ducts and axles are so exposed during the car build-up process on a Wednesday and Thursday at Grands Prix. It transpires that an engineer left Ferrari for another team and the trick was revealed, with immediate queries from their new team to the FIA in a clarification request if this was legal. Clearly the FIA response was negative and Ferrari was told to remove the ducted set-up.
Of course, moveable bodywork is banned and any simple means to close the duct into the hollow axle when the car is steered would have been evident to the scrutineers and rivals, so the effect had to be more covert. A paddock source confirmed that Ferrari was using this trick and that movable flap valves were used inside the brake duct to create the on-off effect. In a straight line, the duct would be closed and no flow would be passed through the axle, but as the car starts to turn and the lateral G-force builds up, the flap valves opened under the load and the duct started blowing through the axle.

What Ferrari was trying to achieve was a mix of downforce and drag reduction. On the straights, the unblown axles would do less to prevent the tyre wake upsetting the rear aero, so the rear wing ran in dirty air, creating less downforce, but crucially less drag. Then through the corners, the flaps open and the duct blows through the axles, pushing the tyre wake away from the rear end and making it create downforce again.
Quite how Ferrari sought to justify this system will no doubt remain a secret, perhaps citing the set-up as part of the suspension, therefore responding to car loads and thus escaping the movable bodywork regulations.
Regardless, it was rightfully outlawed and has been removed from the car since mid-season, and this will have cost Ferrari some efficiency.
Ferrari’s flexible floor blade
Another hit for Ferrari apparently occurred around the same time, when the team had to alter the SF70-H’s floor edge at the FIA’s request. During the opening Grands Prix Ferrari’s floor edge was clearly flapping as the car lapped the track. A small aero detail created a fin along the floor’s edge; similar fins are run by all teams in this area.

As the airflow splits left and right around the sidepods, the T-tray splitter and bargeboards push the airflow out wide around the car. The floor outboard of the sidepod is shaped to help the air under the floor escape and flow along the floor’s edge. Shapes used here can be curled edges, flaps above the floor, and this year teams have slotted the floor’s edge to create a stronger effect to direct the air out from under the floor.
The rules demand than any opening in the floor does not form a hole, but rather an opening linked to the floor’s edge. Teams routinely stretch this rule by creating a slot in the floor, which then is made legal by making a cut between the slot and floor’s edge. These cuts can be tiny and barely visible until close-up inspection, but have been accepted by the FIA for many years.

Ferrari’s floor edge fin was slightly different. Rather than a ‘slot and cut’ floor edge, the detail was more like a knife blade joining the floor at the front and being open at the rear. In many respects, this was more in keeping with the spirit of the regulations, as opposed to the typical ‘slot and cut’ approach. However, the long blade shape formed in the floor was poorly supported and not stiff enough. Consequently, it could be seen flapping from the turbulent air passing around it. It is unlikely that this flapping was some form of aero trickery, but rather an unexpected side effect of the design. Despite being stiffened with metal inserts, the unsupported blade shape was still not stiff enough to please the FIA.
For the Austrian GP, the blade design was altered and instead the more typical ‘slot and cut’ design was installed; it is debatable as to whether Ferrari felt any performance impact from this small change.
Red Bull’s flexible wing

Red Bull has been scrutinised for flexible aero since 2009, and many times we have seen wings deforming at speed in order boost its prospects to negate any power disadvantage it had. An update in Austria brought a new front wing endplate design, this being unusual as the footplate running along the edge of the endplate was not parallel to the car’s floor, rather rising upwards towards the front of the car. Another part of this wing update was that the vane mounted to the edge of the endplate was much more undercut than before, only joined to the front for a small portion of its length.
While these changes could be explained as part of the usual aero development programme controlling the airflow around the front tyres, the effect on track was more complicated than that. At a standstill the wing already looked odd, but this was a visual effect of the sloped footplate, made more confusing by the Red Bull RB13 being set up with a lot of rake. Thus, the car’s nose pointed down, but the endplate sloped up. When at high speed it was clear the angled footplate was sloped upwards at a greater angle than when static in the pitlane. This could be explained by the new undercut endplate vane design allowing the wing to bend down under load at speed.

While the wing met the FIA deflection tests in the scrutineering bay, it is not uncommon for on-track loading to exceed the test loads, allowing a wing to pass the test, but still flex at speed. Red Bull affirmed its wing was legal, but for Silverstone the FIA requested it be stiffened up and as a result the Silverstone spec of the wing included a metal support between the endplate vane and the wing. This support met the FIA’s requirements and certainly tied the two surfaces together, albeit the choice of a long thin support did not look like a structurally efficient way to prevent further movement, as the cantilever design would naturally bend under load. This endplate, with its stiffening support, is still being run on the RB13 without problem.
Stay tuned to GPUpdate.net for more technical insight from Craig Scarborough through 2017
Source :http://feeds.gpupdate.net